4. The system should be capable to deal many unexpected situations and keep the workstation running. Those unexpected situations are:
There is no white paper covered on PCB
There are two or more white papers stick together
When the system couldn’t detect the orientation and displacement of PCB due to the defects of PCB itself.
When PCB or white paper is dropped from vacuum suction cup while they are moving with robot, the system should be capable of dealing with this situation and keep the workstation running.
5. The system cycle time should be less than 30 seconds without including the processing time of laser marking.
Procedures:
1. Define the customer’s requirements
2. Determine the suitable robot for the system
3. Layout the workstation
4. Design and analysis the vacuum suction cups
5. Using CCD to tell from the difference between PCB and white paper
6. Find the general rule for all different types of PCB so CCD can use pattern recognition to realize the orientation angle and displacement of PCB.
7. Apply Wise-Tech Robot special technique to detect the total height of PCB and white paper inside the tray.
8. Design the best motion path of Robot
9. Simulate the unexpected scenarios and determine the procedures for trouble shooting.
10. Coding for workstation control computer and robot controller respectively
11. Improve the working procedure and the speed of robot to make cycle less than 30 seconds.
12. Test and Verify the system and make sure the stability and reliability
Results:
Wise Tech Robot received purchase order on 05/23/17 and completed the system on 10/13/17. And after about two-month tuning and debugging, TCI accept the system on 12/19/2017. The system has performed successfully and stably 24 hrs per day until now. The cycle time is 18 seconds only, which is much less than the original requirement 30 seconds by TCI.
The demonstration of the system is shown as the following video.
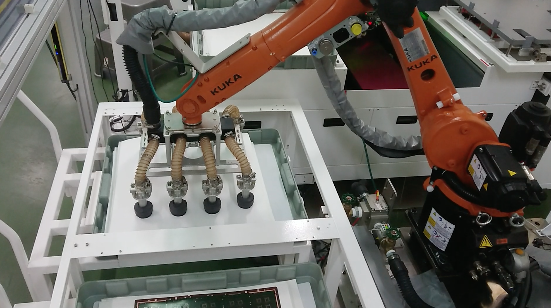